The right software for every weighing application
Whether vehicle scales, filling or bagging systems, checkweighers, counting scales or shipping or receiving scales - SysTec offers a wide range of standard application software for weighing terminals. Get an overview. For special requirements SysTec offers you programming services or development partnerships. We offer the right software for every weighing application.
Any questions? Our experts will be happy to advise you!
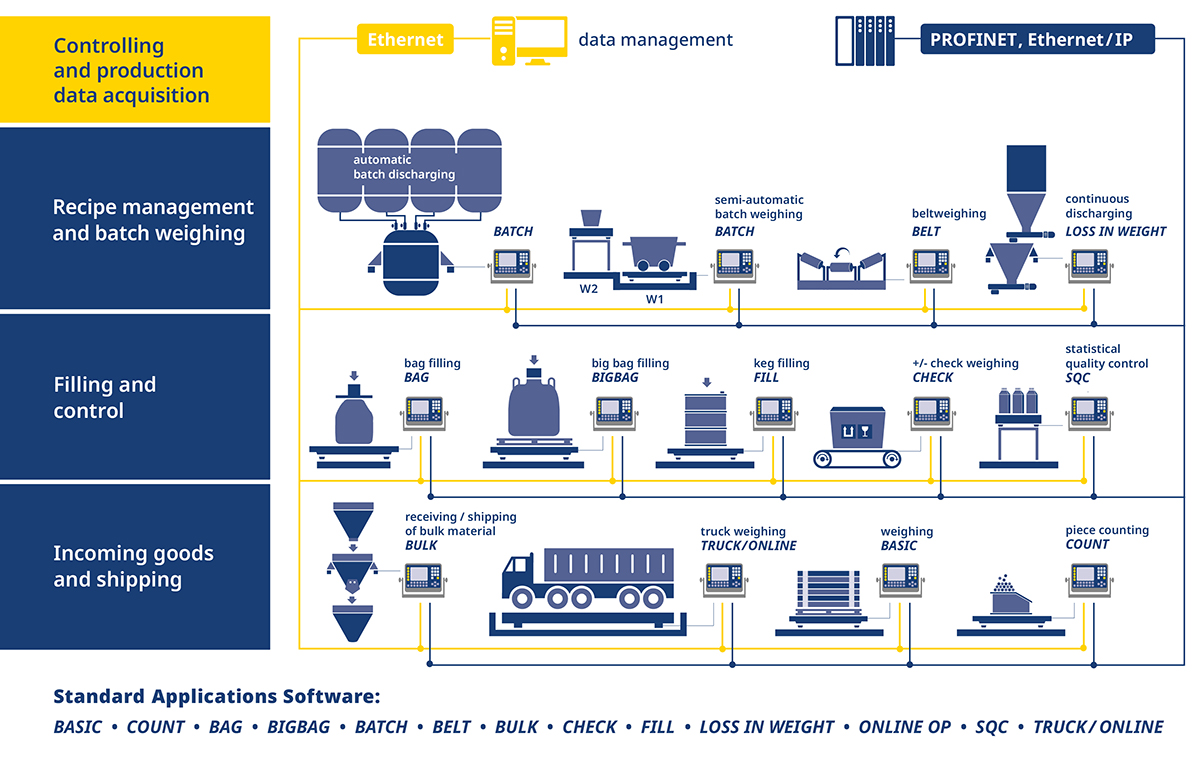
BAG: fill control for automatic bagging aystems
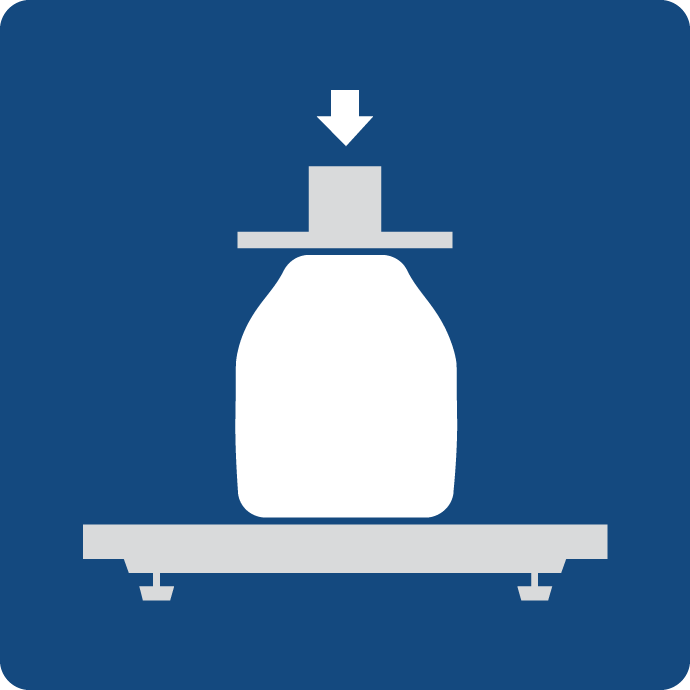
BAG is a universal automatic filling control (AGFI) for use in gravity-fill applications of bulk material into bags.
The controller will connect to load cells or scales of all types and weight ranges including for Ex-area applications, e.g.: floor scales, built-in scales, tension load cells.
Automatic filling of solids
Optionally in gross or net operation
Filling of single bags or batches
- Via dosing screw, dosing slide or vibration chute
- Single or two-stage, optionally with automatic lead time correction
- Batches with preset number of containers or total weight
Typical filling process as gross or net bagging scale
- Product selection – input of target weight (number of bags or total weight)
- Entry of IDs
- Ready status – start filling
- Tare check and/or automatic taring
- Filling with 1 or 2 speeds
- Tolerance weight check and automatic preact adjustment
- Capture of statistical data – optional printout and transmission of gross, tare and net weights, date, time, consec. number, product ID and associated data
- End of sequence, ready for next filling cycle
BIGBAG: filling controller for big bags
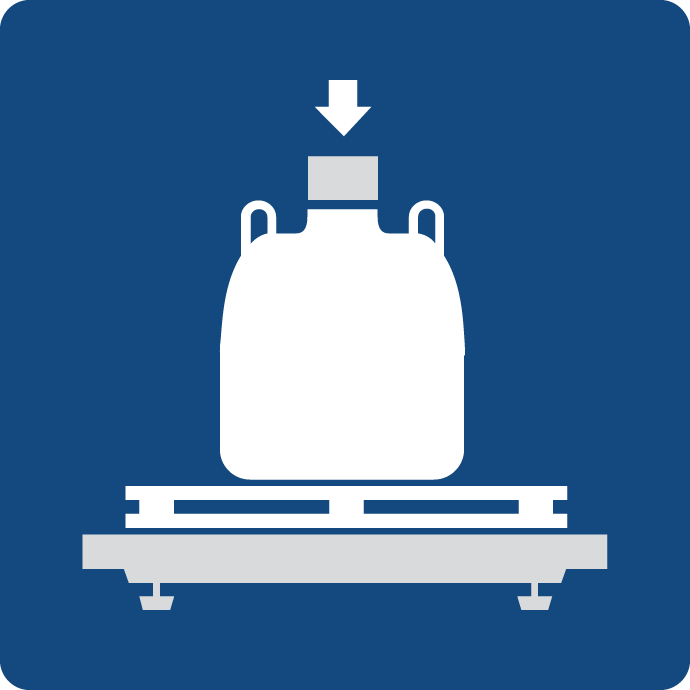
BIGBAG is a universal filling controller for automatic gravimetric filling of big bags and IBCs in W&M approved applications.
The controller connects to load cells or scales of all types and weight ranges including for Ex-area applications, e.g.: floor scales, pit-mounted scales, tension load cells.
Single and multiple bags can be filled in semi or fully automatic operation.
Filling of single bags or batches
- Via dosing screw, dosing slide or vibration chute
- Single or two-stage, optionally with automatic lead time correction
- Control of blower, compression device, etc.
- Batches with preset number of containers or in endless operation
Typical big bag filling cycle:
- Product selection – input of target weight, number of bags and pertaining data
- Attach BigBag to weigher
- Ready status – start fill cycle
- Tare check and/or auto-tare function
- Lift BigBag (manually or with optional software extension)
- Inflate inner bagliner
- Fill with 1 or 2 speeds with simultaneous monitoring of fill time and material flow (option: single or multiple raw material compaction controlled via setpoints)
- Lower BigBag (manually or with optional software extension)
- Tolerance check with auto-preact adjustment
- Capture of statistical data – printout and data transfer of gross, tare and net weights, date, time, consec. number, product ID and associated data – also batch data at batch end
- Message 'Done', 'Ready to start' for next filling
BASIC/COUNT: weighing and piece counting
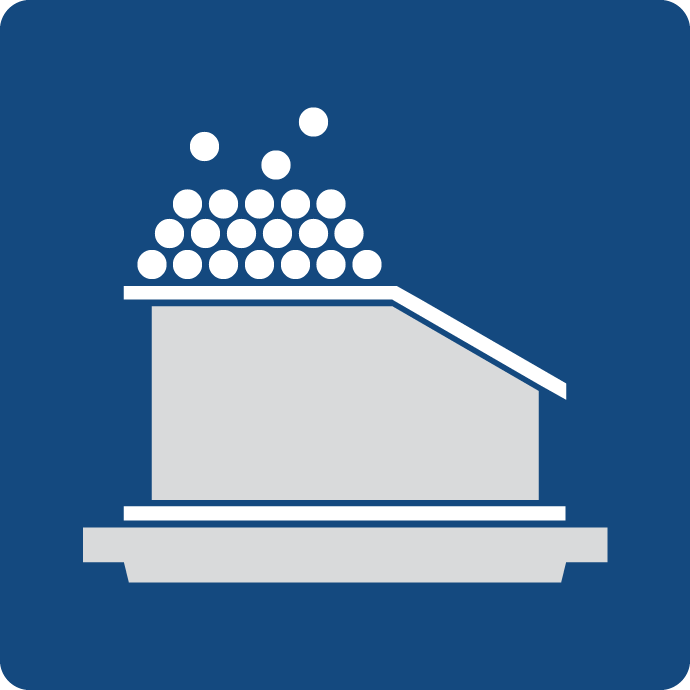
BASIC/COUNT is a W&M approved weighing terminal for capturing of weights, parts counting and checkweighing by weight or piece count
- Up to three scales of any type may be connected to the terminal, e.g. floor, bench or precision scales.
- Parts count is calculated based on preset reference weights or by placing reference parts on the weigh platform
- Parts can be counted by adding parts into an empty container or by removing parts from a filled container
- The bargraph display with changing colors shows the approximation to a chosen target value for checkweighing or counting
Operating modes
- Weighing and Printing (BASIC)
- Plus / minus checkweighing and manual filling by weight and quantity (BASIC and COUNT)
- Piece counting (COUNT)
- Automatic filling of parts (COUNT) from IT6000E
Files
- Article file (1000 entries, IT4000E: max. 10 entries) with article no. and description, target weight and tolerances for +/- check
- Tare file (99 entries, IT4000E: max. 10) with tare no., designation and tare weight
- Label file with different label formats (from IT6000E)
BATCH: multi-ingredient batchweighing control
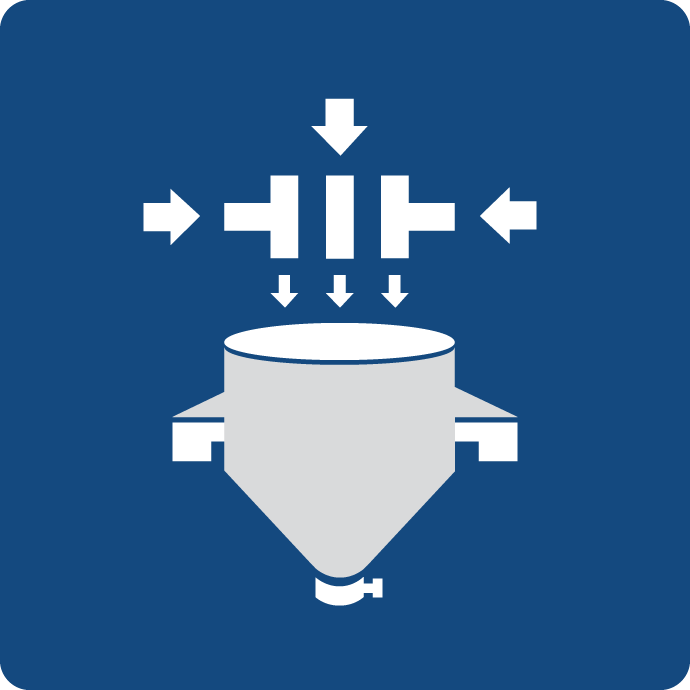
BATCH is a batchweighing controller for automatic weighing of solid and liquid materials in the chemical, pharmaceutical, food and other industries.
The controller connects to load cells or scales of all types and weight ranges, including Ex-area applications.
BATCH is, e.g., suitable for:
- Automatic multi-ingredient batchweighing in hoppers, mixers or tanks
- Recipe batchweighing on floor and pitmounted scales including control of manually added ingredients
- Subtractive batchweighing (weighout) from hopper scales
BATCH is designed for:
- Semi-automatic operation, as stand-alone batchweighing controller with its own recipe and raw material database
- Automatic operation, linked to a process control system or PLC with database maintenance and overall process control.
Sequence and operation are configurable and can be adapted to the requirements of a specific application.
BELT: W&M approved controller for belt scales
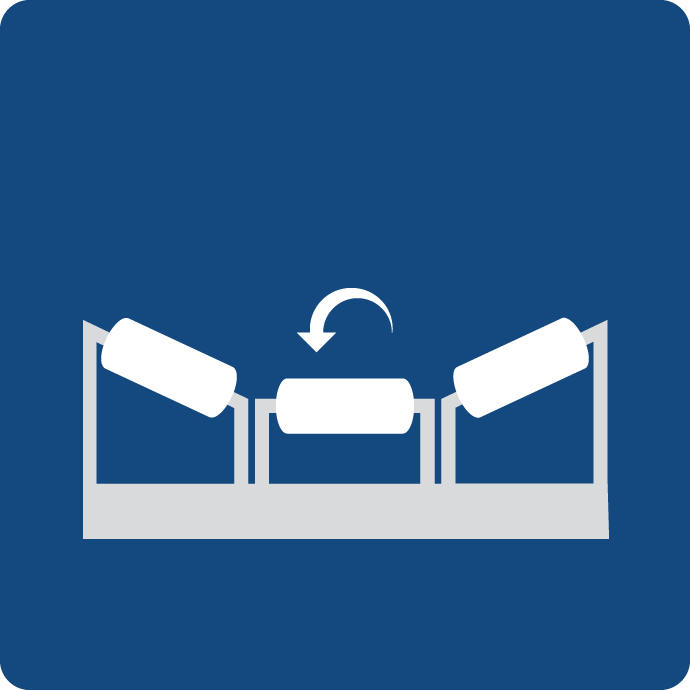
BELT is the application software for capturing continuously the quantity of bulk material conveyed over a belt weigher for both, batching and receiving operations.
It connects to a beltweigher structure with one load receptor with one or several analog load cells.
Controller for belt weigher or feeding tasks:
- For quantity recording or for dosing with preset target weight
- Single user solution or controlled via SPS
Connection
- Incremental encoder for speed measurement
- Digital inputs / outputs
- PLC connection via analog output or Modbus TCP via Ethernet or Profibus, Profinet or Ethernet/IP (option)
- Counter pulse output (option)
- Continuous output (option)
Display
- Main display with current flow rate and process status
- Display of belt load and belt speed and operator prompting
- In batching mode also display of target and remaining quantity
BULK: controller for bulk totalizer and throughput scales
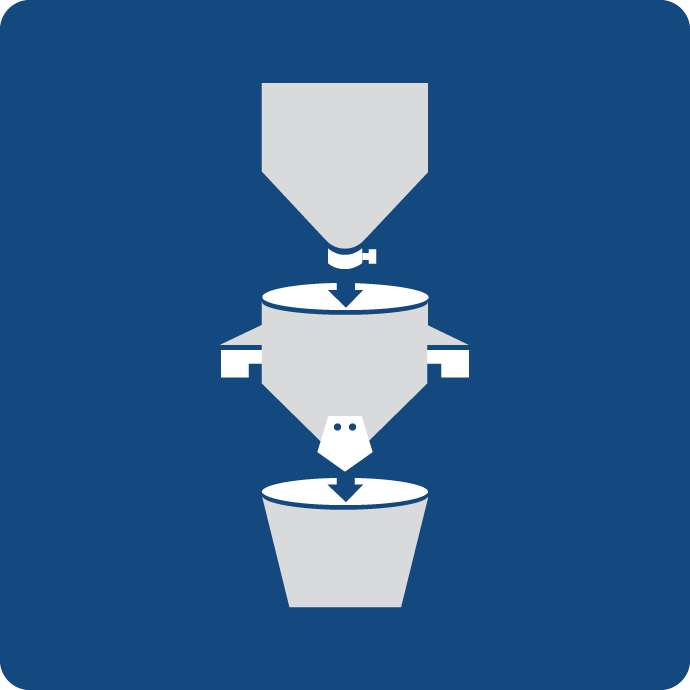
BULK is a universal, W&M approved bulkweighing controller for the shipping and receiving of bulk material. BULK captures the total weight of the incoming bulk material or fills outgoing shipments to a preset target weight.
The controller will connect to all hopper scales or process scales with analog load cells.
Throughput weighing for solids
- Recording the total weight of a delivery
- Filling according to setpoint
Material transport
- Via vibration chute or dosing screw, dosing slide
Dosing flap
- Conveyor with 1 or 2 speeds, with optional flow rate correction
- Monitoring of filling and cycle time
CHECK: check scale application
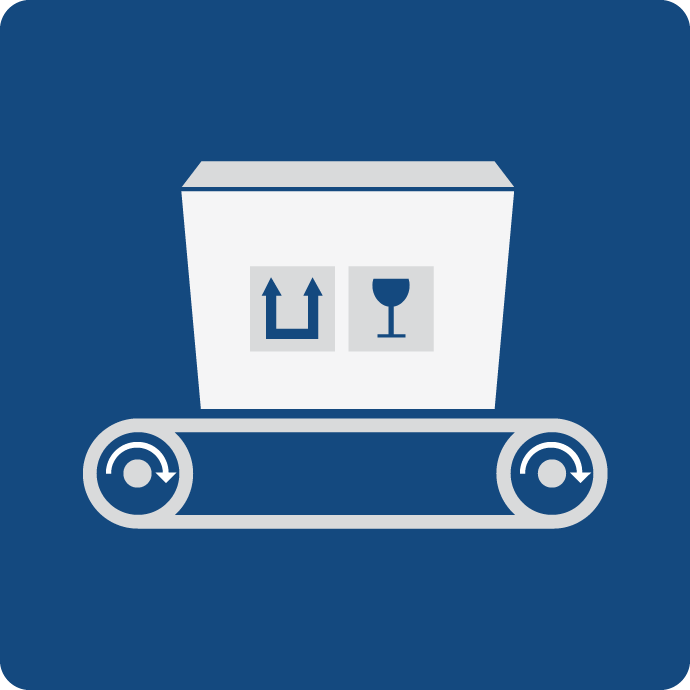
CHECK is the application program for automatic W&M approved control of piece goods. Weighing can be in dynamic or start / stop mode.
- The controller will connect to single-point load cells or 4-load-cell platforms with force introduction according to type approval certificate
- CHECK stores target weights and tolerance zones for up to 99 different products
- The weight check is started via a scalemounted light barrier or after exceeding a preset weight threshold
Typical cycle:
- Product selection – target weight and tolerance zones are preset
- Ready status – start conveyor
- Detection of product with one or two light barriers or by weight threshold, start of checkweighing
- Weight capture, zone classification and entry into statistics file
- Optional printout or transfer of weighing data
- Next checkweighing cycle ...
CONTROL/ONLINE: for remote-controlled weighing terminals
CONLTROL/ONLINE is used for remote control of weighing terminals via Ethernet or serial interface from a PC. Commands for controlling the sequence are sent from the PC program. The PC program always has complete control over the sequence and weighing document printing.
Control commands (example IT8000E CONTROL/ONLINE)
- Capture weight, settled or in motion
- Manual tare
- Autotare
- Show text with/without acknowledgement
- Data entry in response to a displayed operator prompt
- Print gross, net or tare weight
- Read digital inputs
- Set digital outputs on/off
DOS: Single component filling controller
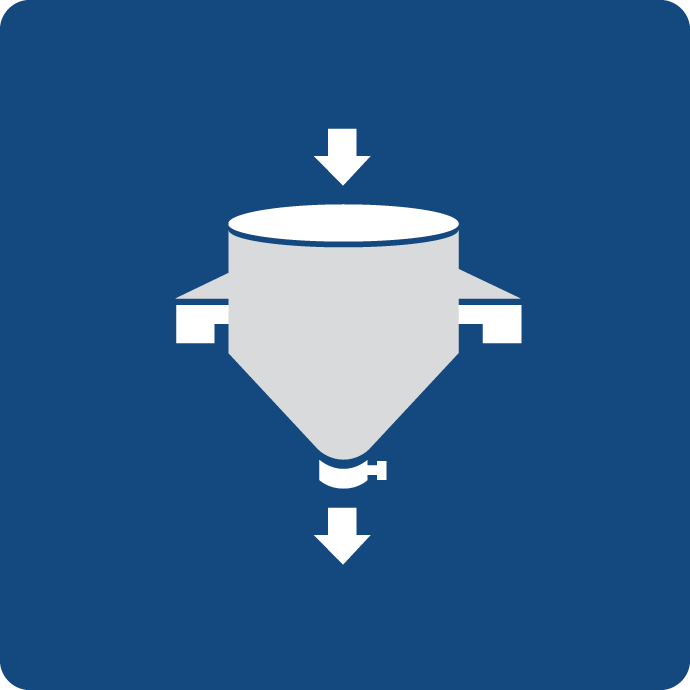
DOS is a universal W&M approved filling controller for use as automatic (AGFI) weighing instrument for the gravimetrical filling of liquid and solid material. It controls the filling process with fast and slow speed via screw or vibratory feeder or filling valve.
DOS is a good basis for creating customer-specific software for single-component filling systems. For this purpose, the DOS software already contains all the relevant software components for a W&M approved automatic scale.
FILL: fill control for automatic liquid filling
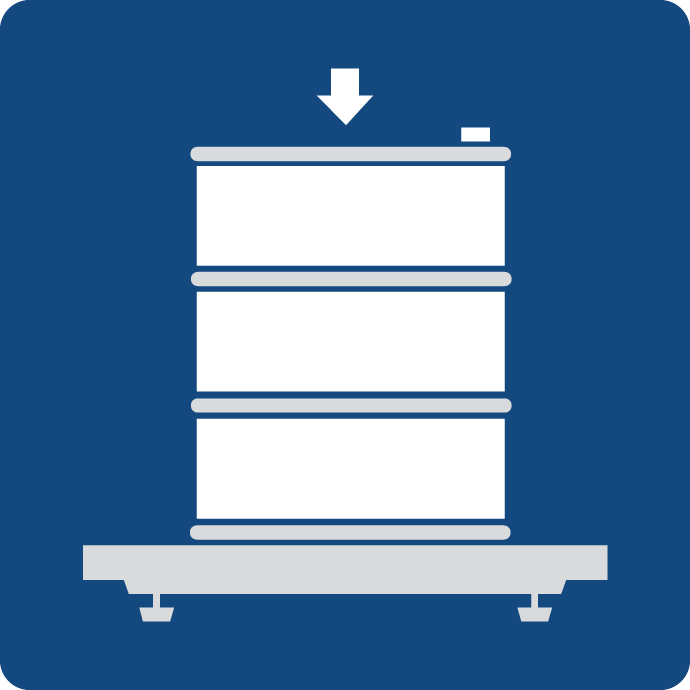
FILL is the application software for automatic filling of liquids into kegs/drums, canisters or containers.
The controller connects to 1 or 2 scales of any type with analog or digital force transducers.
Operation modes:
- Above-surface, below-bung, sub-surface
- Single units and batches can be filled in automatic and semi-automatic operation
Typical keg/drum filling cycle:
- Product selection – input of target weight and number of containers
- Ready status – start fill manually or via external signal
- Tare check and/or auto-tare function
- Lower fill lance (drum with bung-hole)
- Fill in 1 or 2 speeds with simultaneous monitoring of fill time and material flow (when sub-surface operation, fill-lance lift during fill is possible)
- Raise fill lance (drum with bunghole)
- Tolerance weight check with auto-preact adjustment and automatic fill-jog if underweight
- Capture of statistical data – printout and data transfer of gross, tare and net weights, date, time, consec. number, product ID and associated data – also batch data at batch end
- End of sequence, ready for next filling cycle
LOSS IN WEIGHT: controller for constant rate feeders
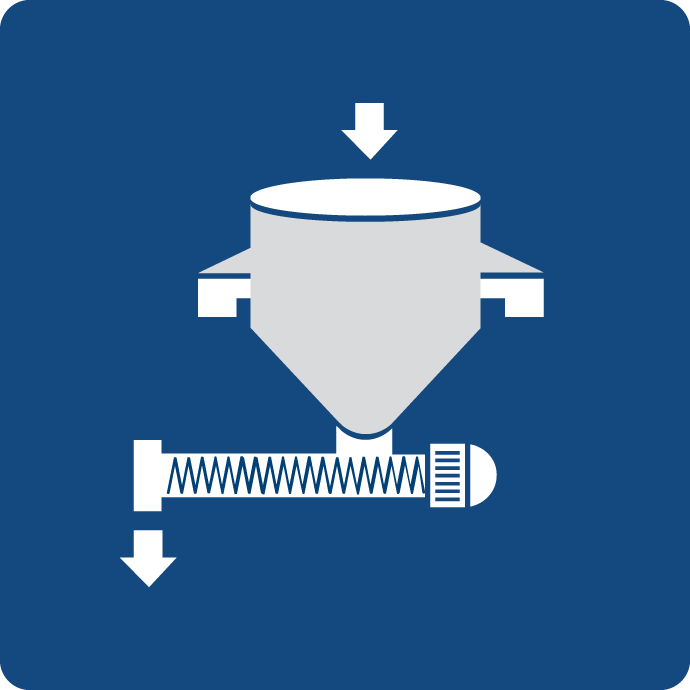
LOSS IN WEIGHT is a controller for loss-in-weight weighing systems used for the discharging of bulk material in continuous processes for food, chemical products, building materials and other
sectors of industry.
LOSS IN WEIGHT connects to analog or digital scales of all types, including Ex-area applications.
It is suited for the continuous supply of product to
- Extruders
- Injection die casting machines
- Continuous mixers
- And other process equipment requiring constant material flow
The raw material is discharged at constant flow rate from the weigh hopper via screw, vibratory or rotary feeder.
LOSS IN WEIGHT controls the feeding device to adjust the actual feed rate to the preset target.
The automatic refilling of the weigh hopper is controlled via selectable setpoints and takes place without interrupting the feeding process.
SQC: statistical quality check
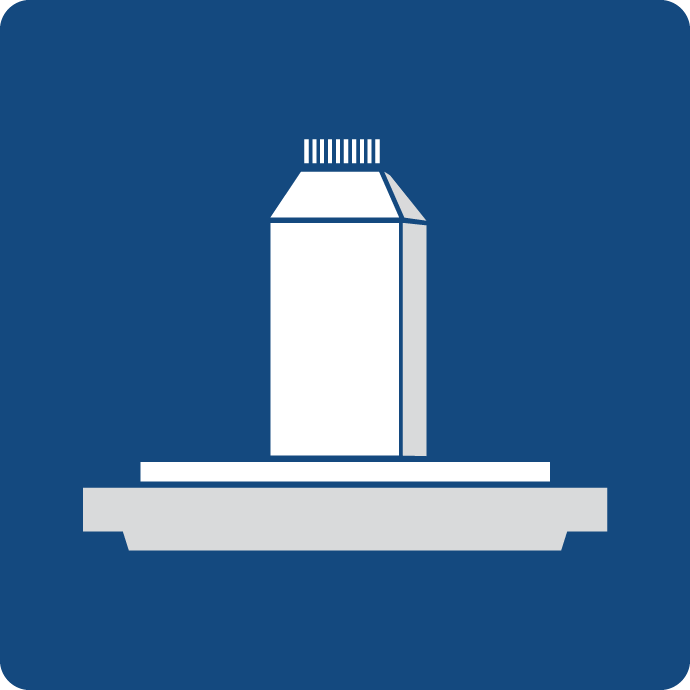
SQC is an application software for capture and evaluation of samples in compliance with the regulations for statistical quality checks. The evaluation method can be selected, either compliant to EC regulations for prepackaged goods or pharmacopeia or with freely chosen limits. Filling quantities can be checked either by weight or by volume.
It supports connection of one or two analog or digital scale base of any type.
Typical check cycle (check method 'Individual'):
- Choose production line
- For new product choose one from product file
- Enter batch data
- Capture weight when threshold is exceeded and start checkweighing
- Assign captured weight to tolerance zone, enter in statistics file
- Capture next sample until complete
- Display and optionally print result of sample
- On end of batch display and optionally print result of batch
- Next cycle ...
TRUCK/ONLINE: for truck scales
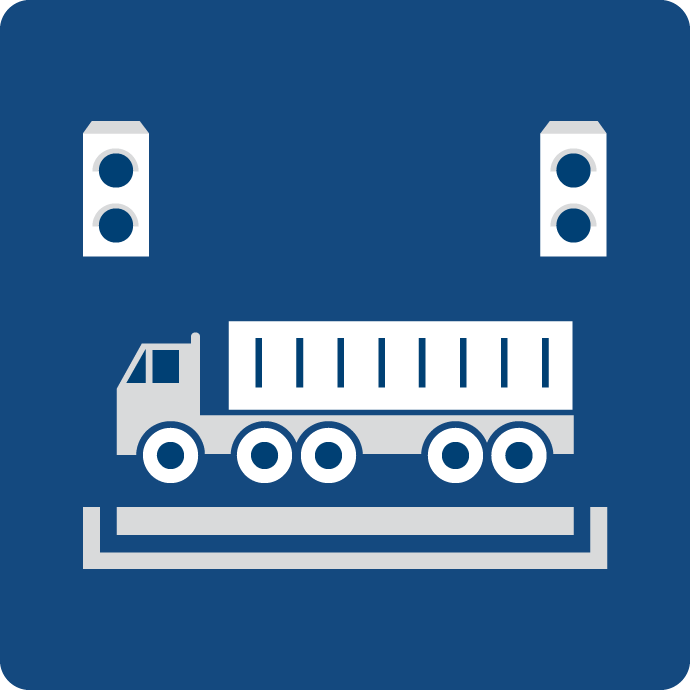
TRUCK/ONLINE is an application software for truck scales.
The weighing terminal can be connected to one or two weighbridges with a total of up to 16 load cells. A facility for selecting individual weighbridges or combining both bridges is provided.
Operating modes
- First weighing with approved storage of gross or tare weight against a 2-digit ID
- Second weighing capturing of gross or tare weight and automatic calculation of net weight. Optionally with axle weighing.
- ONLINE mode with full remote control from PC. Data logging and storage of W&M approved weights in the weighing terminal.
- Axle weighing to capture the weight of up to 8 axles one after the other (optional, not for W&M approved applications)
Typical weighing cycle
- Select first weighing
- Enter license plate number
- Enter additional data, e.g. product number or operator ID
- Weighing with ticket print and storing of first weight against a 2-digit number
- Select second weighing
- Enter 2-digit number of first weighing
- Weighing of second weight with net weight print