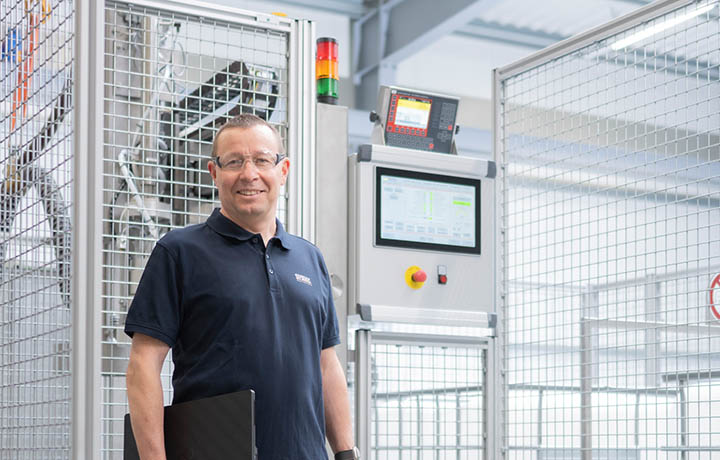
When it comes to challenges in weighing technology and customer-specific application software, Joachim Pauel is the first point of contact for SysTec customers.
He heads SysTec's technical support team and application development. Customers as well as junior SysTec colleagues benefit from his many years of experience in weighing technology.
In the following interview, he describes the application area of filling systems for liquid products and explains the benefits of the SysTec control system.
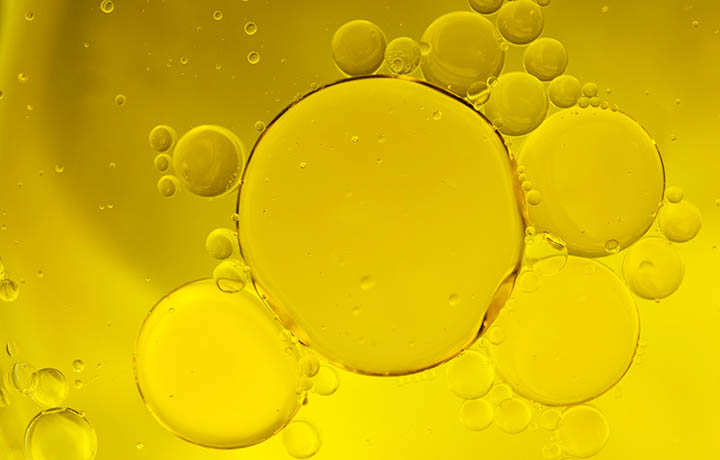
What filling methods do exist for liquids?
There are special containers and filling processes for a wide range of liquids and their specific properties. For foaming liquids with low viscosity, the below-level method is common. This method is also suitable for filling flammable products. There is also the above-level method for viscous liquids that do not foam. The liquid products are usually filled into drums with lids. Liquids can also be filled into bunghole containers using below-bung filling. This method is suitable for non-foaming products with low viscosity.
SysTec offers matching weighing electronics for every task, such as the powerful and flexible IT8000E weighing indicator. We also offer the standard FILL E application software and, of course, customers can ask us to provide a specific software solution.We offer numerous options for the W&M approved filling of a wide variety of liquids into different containers, such as canisters, drums, IBCs or buckets. Single containers and batches can be filled in automatic and semi-automatic mode.
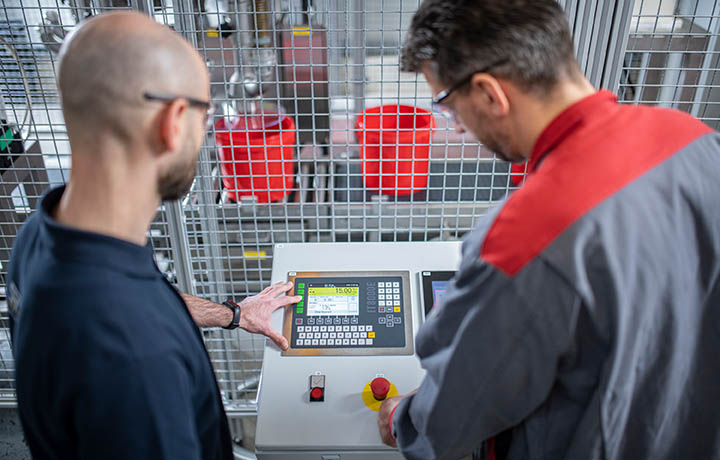
What characterizes SysTec weighing electronics, which are used for filling stations?
Our weighing electronics are W&M approved as automatic weighing instruments for filling (AGFI) – legal standards and requirements are met both nationally and internationally.
Speed and precision are important criteria for filling processes. SysTec weighing indicators are characterized by a high throughput rate due to precise filling based on fast signal processing. One or two scales of different designs with analog or digital load cells can be connected.
For many system integrators who use our weighing electronics, the PLC connection via fieldbus or Modbus TCP is also an important feature; as well as the easy connection to third-party systems such as labeling machines or other equipment.
Hazardous liquids are often used in the chemical industry. With our ATEX approved weighing indicators, potentially explosive substances can also be filled into a wide range of containers. The devices have a stainless steel housing and comply with ingress protection class IP69K. Thus, filling stations can be operated safely even under difficult environmental conditions at various locations. This also applies to the monitoring of the weighing system.
Beyond that, the SysTec weighing electronics offer valve control for the filling modes below-bunghole, partial below-level, below-level and above-level.
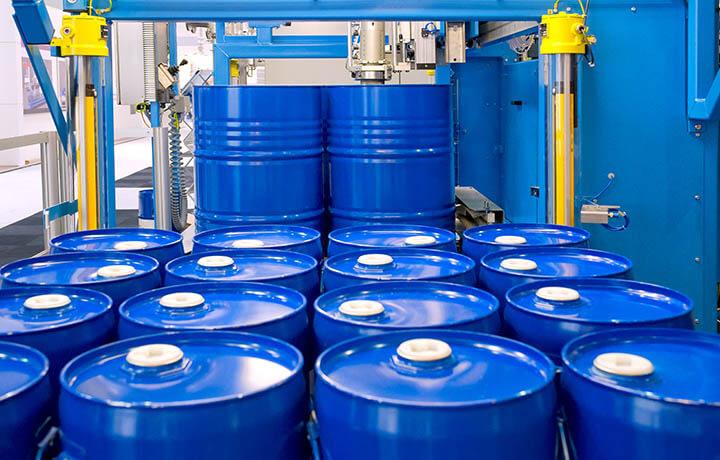
Can you give some specific examples of how the FILL E software is used in practice?
Of course. A large number of well-known customers in various industries have been successfully using our weighing indicators with FILL E software for many years. The range of applications is wide: This includes, for example, the fast and precise filling of canisters (such as 5 kg oil), drums (30 l to 220 l) or IBCs (up to 1000 l).
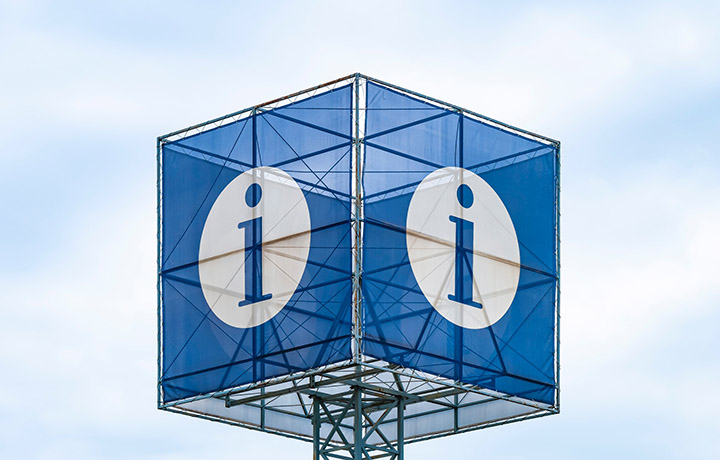
What are the trends in filling systems and what does SysTec offer?
The trend towards digitalization in filling systems has the objective to ensure that all activities can be smoothly coordinated. As part of the Industry 4.0 process, machines and systems communicate with each other. Therefore, it is important to define interfaces in automation technology independently of the manufacturer to allow users to remain flexible. In the Internet of Things, automation components must identify themselves automatically. This also applies to weighing systems. SysTec supports the new OPC UA interface. This allows manufacturer-independent networking of multiple systems. This OPC UA interface will play a major role regarding filling systems in the future.
Our weighing electronics also support the MQTT protocol. Weight values can simply be sent from the SysTec weighing indicators to the MQTT broker. These values can then be received by various end devices (such as computers, smartphones, possibly other brokers, etc.). This gives users greater independence when they choose the location of the filling systems.
Data analysis is becoming increasingly important. SysTec enables collection of data in the cloud. The data can then be analyzed via web interfaces.